On the 8th of July, we were delighted to receive the biz4Biz 'Made in Herts' Manufacturing Award sponsored by Barclays.
Impartial and expertly judged, the biz4Biz awards ceremony is always a highlight in our calendar. On the night, our production team: Shona Tranter, Mark Wildman, Luke Wrangles, Shelley Newson, Charlie Bull, Nick Blair and Samantha Peedle, and the marketing team: Jacqui Riches and Nicola Marques, collected the coveted award.
Mark Wildman, Production Manager, comments,
We were both surprised and honoured to be invited to this year's awards at Tewin Bury Farm. Nobody could have been more surprised than us, when we won. Winning this particular category, and I can speak for everyone in our group, is a wonderful experience. We were up against some seriously impressive, well-established companies from around Hertfordshire, as you can imagine, we thought we only had a slim chance of winning.
The award is welcomed by everyone who has worked tirelessly to make our products the perfect solution for all our clients. This recognition for our dedication and hard work has been an enormous boost. We thank biz4Biz for the award and such a wonderful and fun evening.
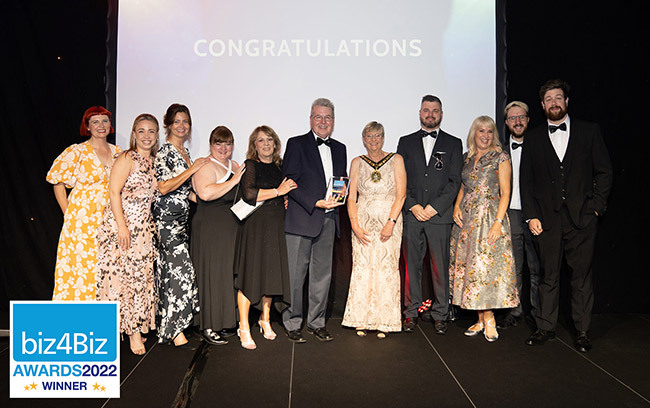
A CLOSER LOOK AT OUR AWARD-WINNING PRODUCTION FACILITY
Mark Wildman, our Production Manager, gives us a closer look at our manufacturing processes at our luminaire factory in Ware, Herts.
Here at CU Phosco, we have a modern manufacturing plant with highly trained employees and logistic support to meet the needs of today's customer demands. However, we can never rest on our laurels as LED, lenses, and the drivers that power them continue to evolve, so we too must evolve with them or, like HID before it, risk falling behind. And we will not permit that to happen.
WHAT DOES AN AVERAGE DAY HERE AT OUR MANUFACTURING PLAN ENTAIL?
At any one time, there is usually the equivalent of three weeks of work in the manufacturing cycle. This allows us to continuously pick, manufacture and deliver orders and gives sufficient flexibility to sort out any procurement issues before manufacturing. The manufacturing schedules are produced in advance so that different departments know what is required of them.
The logistics team manage the picking process so that we can satisfy orders. This is not necessarily as easy as you may think. We have thousands of components, and many of these are derivatives of the same thing, especially when it comes to LED's, drivers and lenses of which there are many variants. The team has to micromanage the process to ensure the correct components are prepared on an order-by-order basis. Some orders have multiple lines, of distinct types, in various quantities, so you can see that it is far from a straightforward process.
Once manufacturing takes ownership of the orders, there are multiple considerations before work starts. For example, arre there any specific requirements? Special colours? Any peripherals? Extra procedures for particular projects and so on.
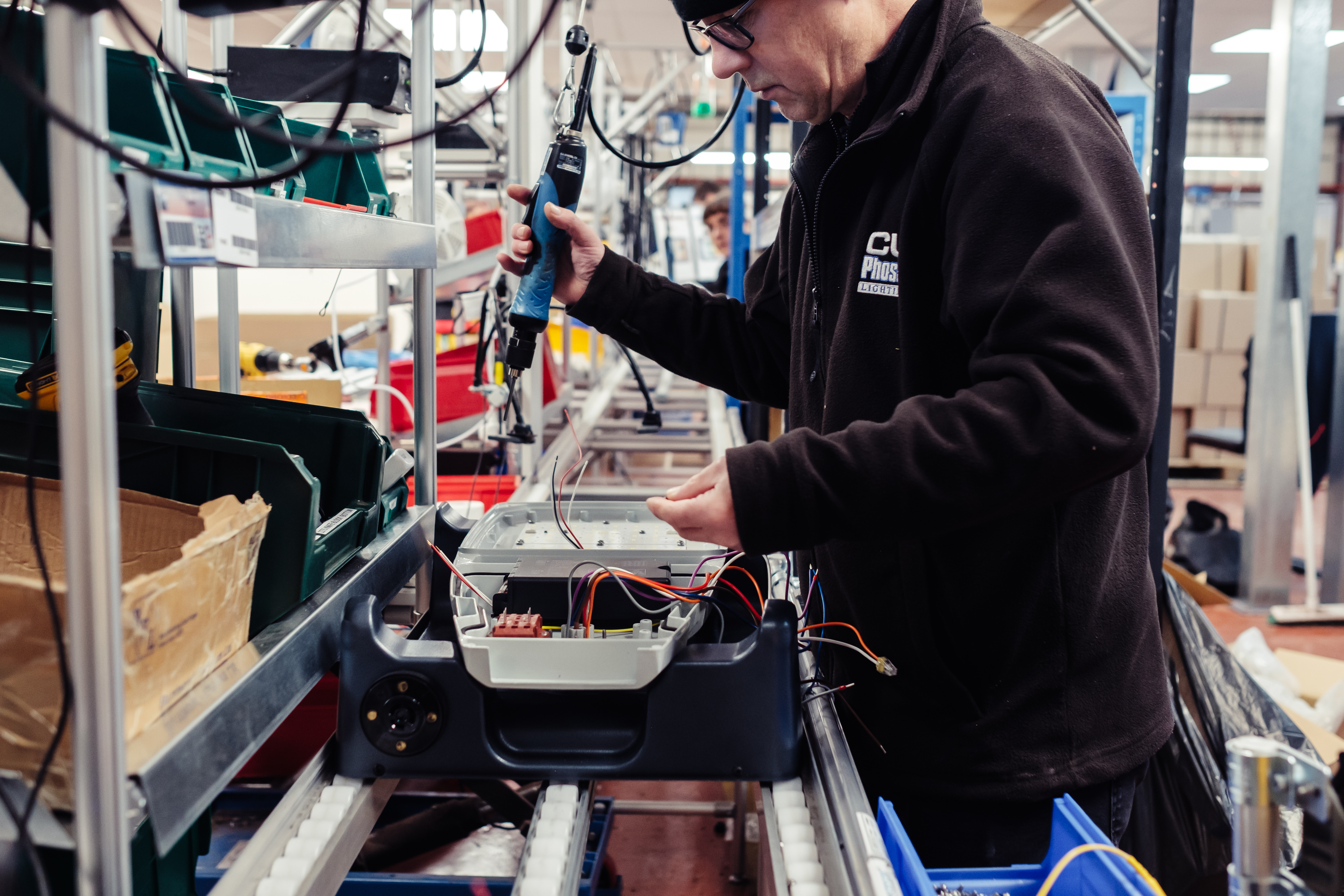
OUR MAINS CABLE PRODUCTION
Chief amongst these are mains cable supply, driver programmes, labels, and the paperwork. We have invested considerably in a cable processing cell and now produce all of our mains and peripheral cables and prepare numerous ANSI dimming receptacles. Most orders require mains cables to be supplied and fitted, and we can control this complete process. We produce any length from half a metre up to and including twenty-two metres in length. So far, we have processed several hundred miles of cable in both 1.5mm² and 2.5mm² grades.
LUMINAIRE DRIVER SETTINGS AND STANDARDS
All of our LED lighting equipment requires a driver, or drivers, to power them, and each driver needs to be programmed to suit each customer's needs. This essentially consists of setting the milliamperage but may also require setting dimming profiles. Without specific instructions from the client, we would programme a file of standard settings and parameters to ensure the lanterns run optimally.
Simultaneously, programme files are produced, and documentation is prepared, including the test sheets, which have all the details and test parameters inserted so that manufacturing runs the appropriate test procedures correctly. Labels with all the necessary information and kite marks are produced, and each lantern has its unique identifying number. Even when dealing with large orders (in the thousands), we can trace each unit down to its individual components for traceability.
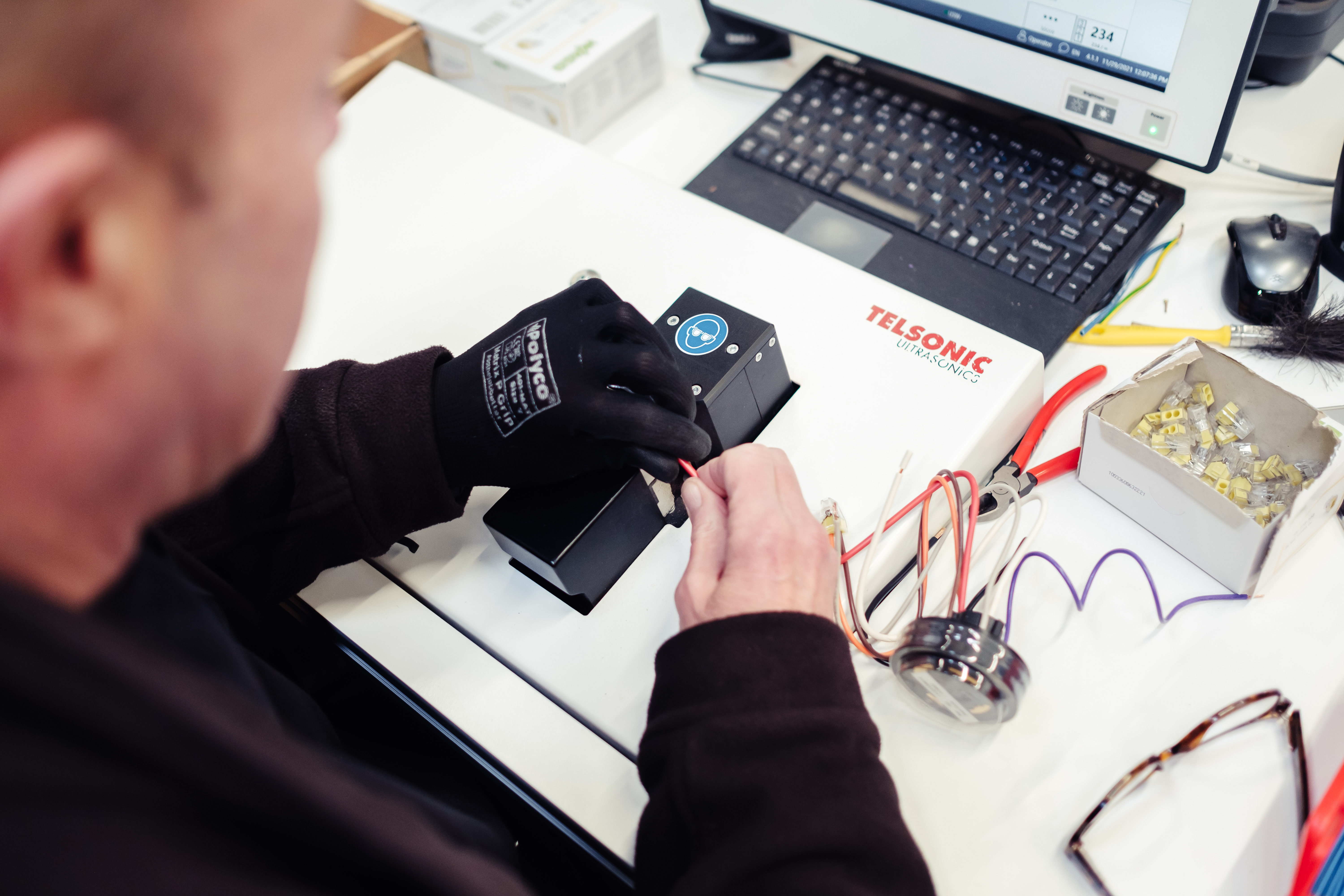
BENCH-BUILT AND ASSEMBLY LINE PRODUCTION
All the documentation and labelling are made into a pack ready for dissemination to the necessary assembly line or bench. It is worth pointing out that although we have numerous assembly lines in place, there is still a need for bench work, particularly for our current heritage range, which is not conducive to volume production. Looking ahead, our heritage range is now under major review, and we look forward to its redevelopment.
Floodlighting is another range that is currently best suited to bench building. However, the newer range, currently in development, may lend itself to line build in the near future.
Whether line built or bench built, the same procedures apply. All of our volume projects and volume orders are manufactured on production lines. The volume work's intensity must be balanced to maintain quality and procedures while meeting the daily targets. Our assembly personnel must be completely focused on the tasks in hand to preserve such exacting standards.
Bench build has a different kind of pressure in that, although targets still have to be met, workers are entirely reliant upon themselves, as individuals, to do the job correctly, which in many ways is more intense than line assembly. Line manufacture is broken into parts so that the individual works on a particular operation on which they can focus. When bench building, the individual is responsible for the entire process, which, however you look at it, is added pressure.
Quality is of the utmost priority throughout the process, and we have a team of employees who will randomly pick finished units at any point to perform a complete check on them to ensure standards are maintained. Additionally, as well as first-off samples, units are checked mid-order and at the end of the order as standard.
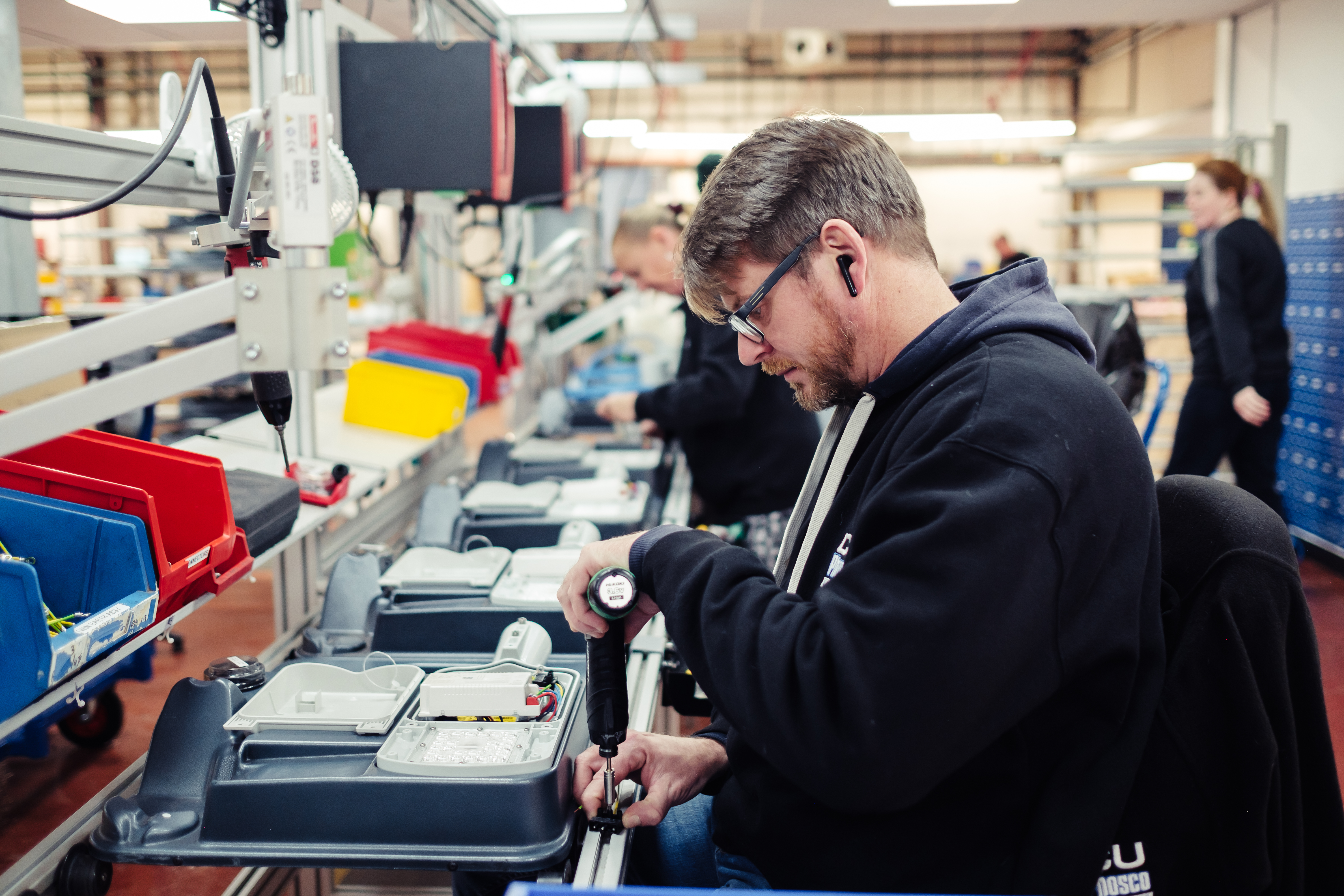
SUSTAINABLE PACKAGING AND OPTIMISED TRANSPORTATION
After the orders are complete, they must be prepared for dispatch. In the case of volume orders, they are invariably packed into large cases, and, of course, quantities vary depending on which lantern is manufactured. This form of packing is very much in demand as packing materials are minimal, and the cases themselves are either recyclable or returnable. However, we still have to resort to conventional palletisation or a simple carton arrangement with smaller orders.
Even then, the mode of onward transportation is carefully considered and needs to be as cost-effective as possible for both the customer and ourselves. Regrettably, at the time of writing, transport costs continue to escalate and fluctuate almost daily and are one of the few things we have little control over. All we can do is continually review these costs, maximise efficiency, and hope for an eventual price downturn so we can pass on reductions to our clients